行業(yè)新聞
汽車先進高強鋼成形技術(shù)應(yīng)用現(xiàn)狀及發(fā)展趨勢
2018年09月06日
隨著能源和環(huán)境問題的日益突出以及人們對汽車安全性能關(guān)注度的持續(xù)增加,在保證安全的前提下實現(xiàn)車身的輕量化正成為汽車工業(yè)的主要發(fā)展方向。在降低油耗、減少排放的諸多措施中,減輕車重的效果是非常明顯的。
鋼鐵、鋁材和塑料是制造汽車的三大材料,其中鋼鐵是汽車車體的主要材料,也是性價比最高的材料,而先進高強鋼作為一種優(yōu)秀的車用輕量化材料,其發(fā)展和應(yīng)用為節(jié)能減排提供了重要途徑。采用先進高強度鋼板,可以在達到強度要求的同時,有效減少沖壓件厚度和數(shù)量,從而達到減重的目的;另一方面,采用高強度鋼板更容易達到安全性能指標(biāo)要求。在白車身制造方面,近年來高強鋼板的應(yīng)用及使用比例在不斷提高。
目前的冷沖壓工藝在對高強度鋼板進行成形的方面存在著明顯的不足,易產(chǎn)生開裂、回彈等缺陷,無法滿足產(chǎn)品的要求。熱成形技術(shù)作為一種新型的成形工藝,可以有效地彌補高強度鋼板的成形缺陷,它具有成形能力高、零件回彈小、成形零件強度級別高的優(yōu)點,目前已廣泛應(yīng)用于全球各大汽車公司的多種車型,重點使用在對碰撞要求較高的部位,如圖1所示的汽車門檻、前保險杠橫梁、B柱等。
汽車先進高強鋼在白車身上的應(yīng)用現(xiàn)狀
近年來,國內(nèi)外企業(yè)開始不斷研究并開發(fā)各種先進高強鋼。國際鋼鐵協(xié)會先進高強鋼應(yīng)用指南第三版中,將高強鋼分為傳統(tǒng)高強鋼和先進高強鋼。傳統(tǒng)高強鋼主要包括碳錳鋼、烘烤硬化鋼、高強度無間隙原子鋼和高強度低合金鋼,先進高強鋼主要包括雙相鋼、相變誘發(fā)塑性鋼、馬氏體鋼、復(fù)相鋼、熱成形鋼和孿晶誘發(fā)塑性鋼。
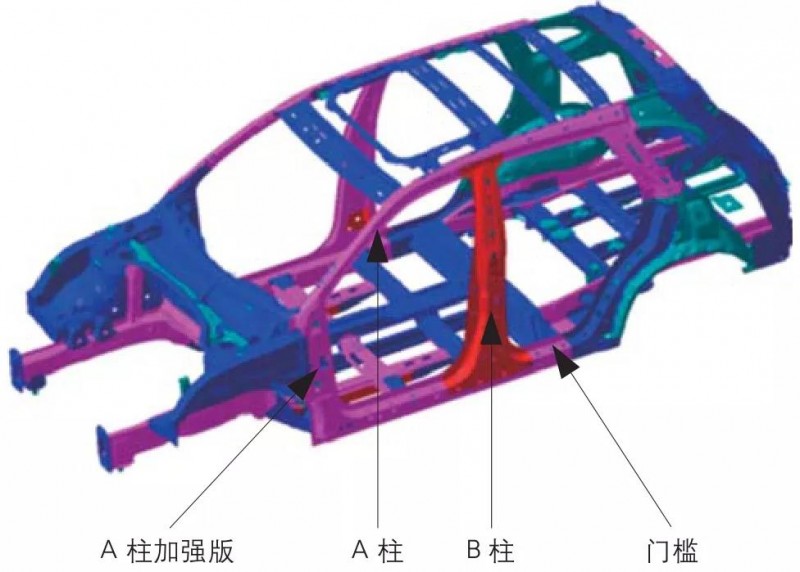
圖1 高強度鋼板在汽車上的應(yīng)用
傳統(tǒng)的高強鋼多是通過固溶、析出和細化晶粒作為主要強化手段,而先進高強鋼是指通過相變進行強化的鋼種,組織中含有馬氏體、貝氏體和殘余奧氏體。汽車用先進高強鋼分為熱軋、冷軋和熱鍍鋅產(chǎn)品,其工藝特點都是通過相變實現(xiàn)強化的。
先進高強鋼的強度(500~1500MPa)和塑性配合優(yōu)于普通高強鋼,同時具有高強度和較好的成形性,特別是加工硬化指數(shù)較高,有利于提高沖撞過程中的能量吸收,所以其在減重和安全性方面具有雙重優(yōu)勢。
汽車先進高強鋼在國外的應(yīng)用現(xiàn)狀
縱觀汽車廠在高強鋼使用方面的發(fā)展,寶馬汽車在歐美地區(qū)發(fā)展速度是較快的。寶馬5系列在不同年代上市的汽車,用料的平均最小屈服強度從1998年版的198MPa增加到2012年版的415MPa,屈服強度在500MPa的高強鋼的使用比例也大幅度增加,寶馬旗下Z4高強鋼板應(yīng)用比例高達55%,而2009款寶馬5系車型從62.1%的比例,提高到了2010年的72%。
日本在高強度汽車板生產(chǎn)和使用方面有明顯優(yōu)勢,日本早在1997年就啟動了“超級鋼鐵材料”的國家研究計劃,為期10年,其主要目的是實現(xiàn)鋼鐵材料的強度翻番,壽命翻番。日本鋼鐵工程控股公司(JFE)在2015年開發(fā)出具有良好延展性和擴孔性的980MPa級高級冷軋鋼板,在業(yè)界屬于首例。目前日本政府主導(dǎo)的科研項目“創(chuàng)新型結(jié)構(gòu)材料研發(fā)”中的子項目“超高張力鋼材開發(fā)”進展順利,其目標(biāo)是在2020年前開發(fā)出抗拉強度1.5GPa和延伸率20%的超高強度鋼板,目前項目中期目標(biāo)抗拉強度1.2GPa和延伸率15%的超高強度鋼板已經(jīng)在實驗室試制成功。另外,美國的通用公司,2004年高強鋼的使用率大幅度上升,低碳鋼的使用率減少至40%,先進高強鋼使用率達到12%,2006年先進高強鋼的使用率已至18%。2016年通用公司旗下全新一代君越車身高強度鋼材比例達到了41%,在A柱、B柱、門檻梁等核心區(qū)域,屈服強度在900~1500MPa的超高強鋼和熱成形鋼大量被應(yīng)用。
先進高強鋼在世界范圍內(nèi)已經(jīng)得到了一定的應(yīng)用,并顯示出在減重、安全和環(huán)保方面的優(yōu)勢。有理由相信,其將成為汽車減重的主要材料。
汽車先進高強鋼在國內(nèi)的應(yīng)用現(xiàn)狀
汽車工業(yè)的發(fā)展、汽車產(chǎn)量和汽車保有量的增加,在給人們出行帶來方便的同時,也產(chǎn)生了油耗、安全和環(huán)保三大問題。為保證汽車工業(yè)的健康發(fā)展,各國制定了相應(yīng)的法規(guī),而各國汽車工業(yè)界認(rèn)為,滿足各項法規(guī)要求較為有效的手段是采用高強度輕量化材料。先進高強鋼其最大的優(yōu)勢就是:提高材料的強度,在所要求的性能不變或略有提高的前提下,減薄板材構(gòu)件的厚度,從而降低構(gòu)件的質(zhì)量。
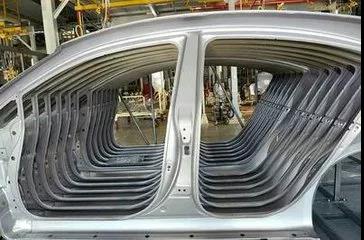
目前,國內(nèi)傳統(tǒng)高強鋼的品種和質(zhì)量與國外的差距不大,相應(yīng)的國家標(biāo)準(zhǔn)已由寶鋼負(fù)責(zé)制定完成。但是先進高強鋼與歐美等發(fā)達國家和地區(qū)還有一定差距,使用的標(biāo)準(zhǔn)也主要是由這些國家制定。近幾年,我國汽車工業(yè)的發(fā)展非常迅猛,整體技術(shù)水平有了很大的提高,先進高強鋼的應(yīng)用也大幅度增加,有利地促進了國內(nèi)先進高強鋼的開發(fā)和生產(chǎn)。目前,寶鋼、鞍鋼、馬鋼等主要鋼鐵企業(yè)都在積極開發(fā)先進高強鋼。其中寶鋼經(jīng)過多年的發(fā)展,已經(jīng)迅速崛起為中國熱沖壓領(lǐng)域的先驅(qū)者。目前,寶鋼已經(jīng)基本掌握了熱沖壓系列核心技術(shù),實現(xiàn)了階段性的跨越式發(fā)展。2007年年底,上海寶鋼熱沖壓零部件有限公司正式成立。2008年上半年,寶鋼建成了以研發(fā)為主兼顧小批量生產(chǎn)的第一條熱沖壓生產(chǎn)線。2009年9月,寶鋼第二條熱沖壓生產(chǎn)線建成投產(chǎn),開發(fā)的抗拉強度為1200MPa和1500MPa的熱沖壓成形鋼,已經(jīng)大量生產(chǎn)供貨。至今,寶鋼已經(jīng)實現(xiàn)向江淮、華晨、奇瑞等汽車廠小批量供貨,用其生產(chǎn)的熱沖壓零件的尺寸精度和力學(xué)性能均已達到行業(yè)先進水平。近幾年,寶鋼正開發(fā)抗拉強度高達1800MPa的熱沖壓成形鋼。
先進高強鋼成形方法簡介
減薄和高強是先進高強鋼在減重和安全方面的優(yōu)勢,但也對沖壓成形工藝提出了新的挑戰(zhàn)。這兩個優(yōu)勢對沖壓工藝而言是惡化成形性的雙重因素,使車身零件在成形過程中易開裂和產(chǎn)生過量回彈,沖壓件的回彈常用U形件的拉深試驗來測定。相對于軟鋼和傳統(tǒng)高強鋼,先進高強鋼的回彈更大,且難以控制,特別是當(dāng)鋼板初始強度大于1000MPa時,傳統(tǒng)的冷沖壓方法就難以生產(chǎn)結(jié)構(gòu)、形狀較復(fù)雜的車身零件,這就需要合適的解決方法。
為解決這一難題,熱沖壓技術(shù)應(yīng)運而生。熱成形工藝就是利用金屬在高溫狀態(tài)下塑性和延展性會迅速增加、屈服強度迅速下降的特點,通過模具使零件成形的工藝。通過對特殊的高強度鋼板加熱到900℃左右,使之易于拉延成形,再經(jīng)過速冷,使鋼板抗拉強度達到1500MPa左右,從而達到零件對超高強度的要求。熱成形工藝流程為:落料--加熱至奧氏體狀態(tài)并保溫--快速放入模具中沖壓成形--保壓定形并淬火--激光切邊、割孔--去氧化皮--涂油(防銹處理)。
先進高強鋼的熱沖壓技術(shù),主要是同濟大學(xué)、哈爾濱工業(yè)大學(xué)、吉林大學(xué)和寶鋼等相關(guān)單位在對熱沖壓技術(shù)、關(guān)鍵設(shè)備進行研究。國內(nèi)大學(xué)研究高強度汽車板熱沖壓工藝,取得成果較多的是同濟大學(xué)機械與材料學(xué)院,主要對熱沖壓過程中,鋼板的加熱溫度與鋼板內(nèi)部組織結(jié)構(gòu)變化模式、沖壓速度、保壓時間、淬火速度、沖壓模具溫度變化等對成形的影響進行模擬研究。
先進高強鋼在白車身開發(fā)中的應(yīng)用及發(fā)展前景
由于汽車未來的市場需求,鋼廠應(yīng)具備制造1000MPa級及以上高強鋼的能力才能適應(yīng)未來市場的需求,才能在減重、節(jié)能、提高安全性、降低排放等方面展現(xiàn)出良好的應(yīng)用前景和好的競爭力。但隨著先進高強鋼的大量應(yīng)用,與過去采用大量軟鋼相比,成形中的起皺、回彈、模具損傷、開裂、翹曲等成形問題和困難大量出現(xiàn)。因此,完善其成形技術(shù)也是下一階段先進高強鋼研發(fā)及應(yīng)用的主要研究任務(wù)。
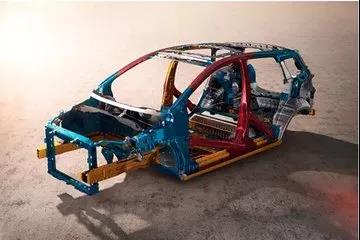
我國先進高強鋼的研發(fā)現(xiàn)狀及發(fā)展趨勢主要如下
⑴ 熱沖壓材料的開發(fā)。目前國內(nèi)各大鋼鐵公司均在進行先進高強鋼的生產(chǎn)和研究,其中最具代表性的企業(yè)主要有寶鋼、鞍鋼、馬鋼等,主要進行強度在1800MPa級及以上的熱沖壓材料開發(fā),同時要在現(xiàn)有強度級別下進一步提升其延伸率,以滿足強度及碰撞要求。
⑵ 防腐蝕性。先進高強鋼在強度和成形性方面展示了良好的應(yīng)用前景,但是在現(xiàn)代汽車工業(yè)中,不僅要采用高強度和先進高強度鋼,同時為保證汽車的防腐蝕性能,還應(yīng)該加大鍍層板的研究和產(chǎn)業(yè)化,并提高鍍層板的品種和質(zhì)量來提高先進高強鋼材料的抗腐蝕性。
⑶ 研究先進高強鋼的熱沖壓成形防止回彈技術(shù)。材料特性決定了其成形工藝,材料的強度越高,成形后零件的回彈越大,防止這種成形缺陷的技術(shù)難度越大,先進的成形方法尤其是防回彈技術(shù)是未來的主要研究方向之一。
⑷ 新型熱成形模具鋼材料的研究開發(fā)。為了有效提高模具熱傳導(dǎo)和抗拉毛特性,增加模具的使用壽命,提高生產(chǎn)節(jié)拍,亟需研究出高導(dǎo)熱、高耐磨、高韌性的熱沖壓模具鋼材料。
⑸ 先進高強鋼熱沖壓成形的模具設(shè)計技術(shù)。在沖壓過程中要使升溫、保溫與降溫過程模具內(nèi)溫度盡量均勻,防止熱應(yīng)力過高而引起模具的損壞;同時要研究熱成形模具模內(nèi)淬火分析和疲勞壽命預(yù)測分析技術(shù),另外沖壓設(shè)備的選擇匹配也是模具設(shè)計的難點。
⑹ 先進高強鋼熱沖壓成形計算機模擬技術(shù)研究。需要解決的關(guān)鍵問題是將先進高強鋼準(zhǔn)確的材料本構(gòu)模型嵌入到數(shù)值模擬軟件中,進而進一步研究高強鋼的熱成形有限元數(shù)值模擬建模技術(shù)。
內(nèi)容來自網(wǎng)絡(luò)
鋼鐵、鋁材和塑料是制造汽車的三大材料,其中鋼鐵是汽車車體的主要材料,也是性價比最高的材料,而先進高強鋼作為一種優(yōu)秀的車用輕量化材料,其發(fā)展和應(yīng)用為節(jié)能減排提供了重要途徑。采用先進高強度鋼板,可以在達到強度要求的同時,有效減少沖壓件厚度和數(shù)量,從而達到減重的目的;另一方面,采用高強度鋼板更容易達到安全性能指標(biāo)要求。在白車身制造方面,近年來高強鋼板的應(yīng)用及使用比例在不斷提高。
目前的冷沖壓工藝在對高強度鋼板進行成形的方面存在著明顯的不足,易產(chǎn)生開裂、回彈等缺陷,無法滿足產(chǎn)品的要求。熱成形技術(shù)作為一種新型的成形工藝,可以有效地彌補高強度鋼板的成形缺陷,它具有成形能力高、零件回彈小、成形零件強度級別高的優(yōu)點,目前已廣泛應(yīng)用于全球各大汽車公司的多種車型,重點使用在對碰撞要求較高的部位,如圖1所示的汽車門檻、前保險杠橫梁、B柱等。
汽車先進高強鋼在白車身上的應(yīng)用現(xiàn)狀
近年來,國內(nèi)外企業(yè)開始不斷研究并開發(fā)各種先進高強鋼。國際鋼鐵協(xié)會先進高強鋼應(yīng)用指南第三版中,將高強鋼分為傳統(tǒng)高強鋼和先進高強鋼。傳統(tǒng)高強鋼主要包括碳錳鋼、烘烤硬化鋼、高強度無間隙原子鋼和高強度低合金鋼,先進高強鋼主要包括雙相鋼、相變誘發(fā)塑性鋼、馬氏體鋼、復(fù)相鋼、熱成形鋼和孿晶誘發(fā)塑性鋼。
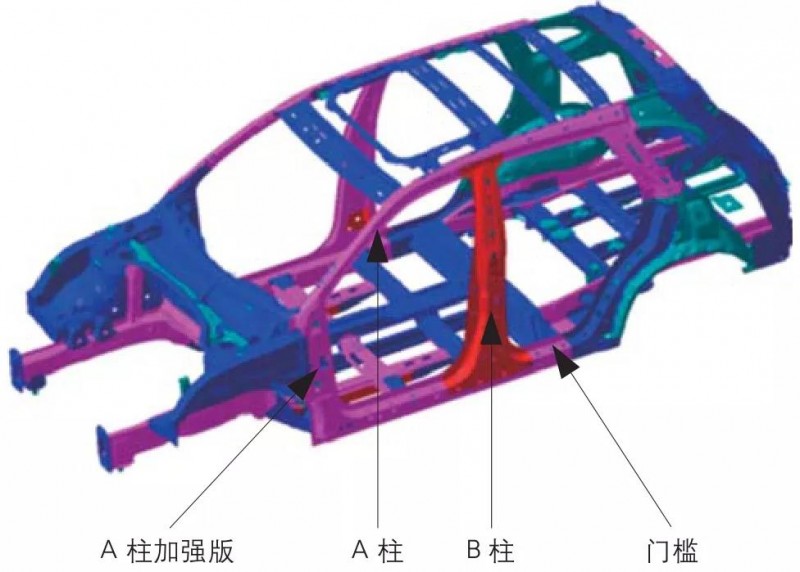
圖1 高強度鋼板在汽車上的應(yīng)用
傳統(tǒng)的高強鋼多是通過固溶、析出和細化晶粒作為主要強化手段,而先進高強鋼是指通過相變進行強化的鋼種,組織中含有馬氏體、貝氏體和殘余奧氏體。汽車用先進高強鋼分為熱軋、冷軋和熱鍍鋅產(chǎn)品,其工藝特點都是通過相變實現(xiàn)強化的。
先進高強鋼的強度(500~1500MPa)和塑性配合優(yōu)于普通高強鋼,同時具有高強度和較好的成形性,特別是加工硬化指數(shù)較高,有利于提高沖撞過程中的能量吸收,所以其在減重和安全性方面具有雙重優(yōu)勢。
汽車先進高強鋼在國外的應(yīng)用現(xiàn)狀
縱觀汽車廠在高強鋼使用方面的發(fā)展,寶馬汽車在歐美地區(qū)發(fā)展速度是較快的。寶馬5系列在不同年代上市的汽車,用料的平均最小屈服強度從1998年版的198MPa增加到2012年版的415MPa,屈服強度在500MPa的高強鋼的使用比例也大幅度增加,寶馬旗下Z4高強鋼板應(yīng)用比例高達55%,而2009款寶馬5系車型從62.1%的比例,提高到了2010年的72%。
日本在高強度汽車板生產(chǎn)和使用方面有明顯優(yōu)勢,日本早在1997年就啟動了“超級鋼鐵材料”的國家研究計劃,為期10年,其主要目的是實現(xiàn)鋼鐵材料的強度翻番,壽命翻番。日本鋼鐵工程控股公司(JFE)在2015年開發(fā)出具有良好延展性和擴孔性的980MPa級高級冷軋鋼板,在業(yè)界屬于首例。目前日本政府主導(dǎo)的科研項目“創(chuàng)新型結(jié)構(gòu)材料研發(fā)”中的子項目“超高張力鋼材開發(fā)”進展順利,其目標(biāo)是在2020年前開發(fā)出抗拉強度1.5GPa和延伸率20%的超高強度鋼板,目前項目中期目標(biāo)抗拉強度1.2GPa和延伸率15%的超高強度鋼板已經(jīng)在實驗室試制成功。另外,美國的通用公司,2004年高強鋼的使用率大幅度上升,低碳鋼的使用率減少至40%,先進高強鋼使用率達到12%,2006年先進高強鋼的使用率已至18%。2016年通用公司旗下全新一代君越車身高強度鋼材比例達到了41%,在A柱、B柱、門檻梁等核心區(qū)域,屈服強度在900~1500MPa的超高強鋼和熱成形鋼大量被應(yīng)用。
先進高強鋼在世界范圍內(nèi)已經(jīng)得到了一定的應(yīng)用,并顯示出在減重、安全和環(huán)保方面的優(yōu)勢。有理由相信,其將成為汽車減重的主要材料。
汽車先進高強鋼在國內(nèi)的應(yīng)用現(xiàn)狀
汽車工業(yè)的發(fā)展、汽車產(chǎn)量和汽車保有量的增加,在給人們出行帶來方便的同時,也產(chǎn)生了油耗、安全和環(huán)保三大問題。為保證汽車工業(yè)的健康發(fā)展,各國制定了相應(yīng)的法規(guī),而各國汽車工業(yè)界認(rèn)為,滿足各項法規(guī)要求較為有效的手段是采用高強度輕量化材料。先進高強鋼其最大的優(yōu)勢就是:提高材料的強度,在所要求的性能不變或略有提高的前提下,減薄板材構(gòu)件的厚度,從而降低構(gòu)件的質(zhì)量。
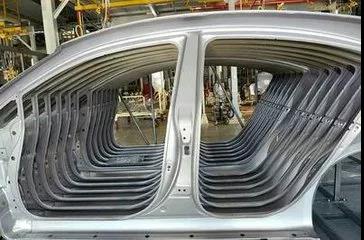
目前,國內(nèi)傳統(tǒng)高強鋼的品種和質(zhì)量與國外的差距不大,相應(yīng)的國家標(biāo)準(zhǔn)已由寶鋼負(fù)責(zé)制定完成。但是先進高強鋼與歐美等發(fā)達國家和地區(qū)還有一定差距,使用的標(biāo)準(zhǔn)也主要是由這些國家制定。近幾年,我國汽車工業(yè)的發(fā)展非常迅猛,整體技術(shù)水平有了很大的提高,先進高強鋼的應(yīng)用也大幅度增加,有利地促進了國內(nèi)先進高強鋼的開發(fā)和生產(chǎn)。目前,寶鋼、鞍鋼、馬鋼等主要鋼鐵企業(yè)都在積極開發(fā)先進高強鋼。其中寶鋼經(jīng)過多年的發(fā)展,已經(jīng)迅速崛起為中國熱沖壓領(lǐng)域的先驅(qū)者。目前,寶鋼已經(jīng)基本掌握了熱沖壓系列核心技術(shù),實現(xiàn)了階段性的跨越式發(fā)展。2007年年底,上海寶鋼熱沖壓零部件有限公司正式成立。2008年上半年,寶鋼建成了以研發(fā)為主兼顧小批量生產(chǎn)的第一條熱沖壓生產(chǎn)線。2009年9月,寶鋼第二條熱沖壓生產(chǎn)線建成投產(chǎn),開發(fā)的抗拉強度為1200MPa和1500MPa的熱沖壓成形鋼,已經(jīng)大量生產(chǎn)供貨。至今,寶鋼已經(jīng)實現(xiàn)向江淮、華晨、奇瑞等汽車廠小批量供貨,用其生產(chǎn)的熱沖壓零件的尺寸精度和力學(xué)性能均已達到行業(yè)先進水平。近幾年,寶鋼正開發(fā)抗拉強度高達1800MPa的熱沖壓成形鋼。
先進高強鋼成形方法簡介
減薄和高強是先進高強鋼在減重和安全方面的優(yōu)勢,但也對沖壓成形工藝提出了新的挑戰(zhàn)。這兩個優(yōu)勢對沖壓工藝而言是惡化成形性的雙重因素,使車身零件在成形過程中易開裂和產(chǎn)生過量回彈,沖壓件的回彈常用U形件的拉深試驗來測定。相對于軟鋼和傳統(tǒng)高強鋼,先進高強鋼的回彈更大,且難以控制,特別是當(dāng)鋼板初始強度大于1000MPa時,傳統(tǒng)的冷沖壓方法就難以生產(chǎn)結(jié)構(gòu)、形狀較復(fù)雜的車身零件,這就需要合適的解決方法。
為解決這一難題,熱沖壓技術(shù)應(yīng)運而生。熱成形工藝就是利用金屬在高溫狀態(tài)下塑性和延展性會迅速增加、屈服強度迅速下降的特點,通過模具使零件成形的工藝。通過對特殊的高強度鋼板加熱到900℃左右,使之易于拉延成形,再經(jīng)過速冷,使鋼板抗拉強度達到1500MPa左右,從而達到零件對超高強度的要求。熱成形工藝流程為:落料--加熱至奧氏體狀態(tài)并保溫--快速放入模具中沖壓成形--保壓定形并淬火--激光切邊、割孔--去氧化皮--涂油(防銹處理)。
先進高強鋼的熱沖壓技術(shù),主要是同濟大學(xué)、哈爾濱工業(yè)大學(xué)、吉林大學(xué)和寶鋼等相關(guān)單位在對熱沖壓技術(shù)、關(guān)鍵設(shè)備進行研究。國內(nèi)大學(xué)研究高強度汽車板熱沖壓工藝,取得成果較多的是同濟大學(xué)機械與材料學(xué)院,主要對熱沖壓過程中,鋼板的加熱溫度與鋼板內(nèi)部組織結(jié)構(gòu)變化模式、沖壓速度、保壓時間、淬火速度、沖壓模具溫度變化等對成形的影響進行模擬研究。
先進高強鋼在白車身開發(fā)中的應(yīng)用及發(fā)展前景
由于汽車未來的市場需求,鋼廠應(yīng)具備制造1000MPa級及以上高強鋼的能力才能適應(yīng)未來市場的需求,才能在減重、節(jié)能、提高安全性、降低排放等方面展現(xiàn)出良好的應(yīng)用前景和好的競爭力。但隨著先進高強鋼的大量應(yīng)用,與過去采用大量軟鋼相比,成形中的起皺、回彈、模具損傷、開裂、翹曲等成形問題和困難大量出現(xiàn)。因此,完善其成形技術(shù)也是下一階段先進高強鋼研發(fā)及應(yīng)用的主要研究任務(wù)。
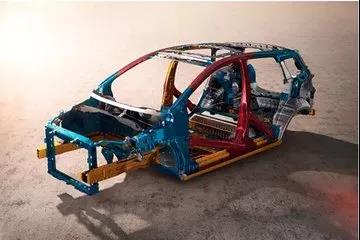
我國先進高強鋼的研發(fā)現(xiàn)狀及發(fā)展趨勢主要如下
⑴ 熱沖壓材料的開發(fā)。目前國內(nèi)各大鋼鐵公司均在進行先進高強鋼的生產(chǎn)和研究,其中最具代表性的企業(yè)主要有寶鋼、鞍鋼、馬鋼等,主要進行強度在1800MPa級及以上的熱沖壓材料開發(fā),同時要在現(xiàn)有強度級別下進一步提升其延伸率,以滿足強度及碰撞要求。
⑵ 防腐蝕性。先進高強鋼在強度和成形性方面展示了良好的應(yīng)用前景,但是在現(xiàn)代汽車工業(yè)中,不僅要采用高強度和先進高強度鋼,同時為保證汽車的防腐蝕性能,還應(yīng)該加大鍍層板的研究和產(chǎn)業(yè)化,并提高鍍層板的品種和質(zhì)量來提高先進高強鋼材料的抗腐蝕性。
⑶ 研究先進高強鋼的熱沖壓成形防止回彈技術(shù)。材料特性決定了其成形工藝,材料的強度越高,成形后零件的回彈越大,防止這種成形缺陷的技術(shù)難度越大,先進的成形方法尤其是防回彈技術(shù)是未來的主要研究方向之一。
⑷ 新型熱成形模具鋼材料的研究開發(fā)。為了有效提高模具熱傳導(dǎo)和抗拉毛特性,增加模具的使用壽命,提高生產(chǎn)節(jié)拍,亟需研究出高導(dǎo)熱、高耐磨、高韌性的熱沖壓模具鋼材料。
⑸ 先進高強鋼熱沖壓成形的模具設(shè)計技術(shù)。在沖壓過程中要使升溫、保溫與降溫過程模具內(nèi)溫度盡量均勻,防止熱應(yīng)力過高而引起模具的損壞;同時要研究熱成形模具模內(nèi)淬火分析和疲勞壽命預(yù)測分析技術(shù),另外沖壓設(shè)備的選擇匹配也是模具設(shè)計的難點。
⑹ 先進高強鋼熱沖壓成形計算機模擬技術(shù)研究。需要解決的關(guān)鍵問題是將先進高強鋼準(zhǔn)確的材料本構(gòu)模型嵌入到數(shù)值模擬軟件中,進而進一步研究高強鋼的熱成形有限元數(shù)值模擬建模技術(shù)。
內(nèi)容來自網(wǎng)絡(luò)
AMTS 2019 第十五屆上海國際汽車制造技術(shù)與裝備及材料展覽會將于2019年7月3-6日在上海舉行,將匯聚來自中國/亞洲的知名汽車制造商和一級供應(yīng)商的工程技術(shù)人員和決策者到場參觀,預(yù)計將有來自世界各地800家展商參展,吸引80,000專業(yè)觀眾到場參觀。
點擊此處,申請2019展位
獲取更多展會信息:
郵箱:info@for-expo.com
電話:86-21-6468 1300/6468 1550
點擊此處,申請2019展位
獲取更多展會信息:
郵箱:info@for-expo.com
電話:86-21-6468 1300/6468 1550
展會快訊免費訂閱
行業(yè)資訊,展會新聞,實時更新
聯(lián)系我們
展商服務(wù)
電話:
86-21-22317397